Setting the foundation for Software-Defined Verification and Validation
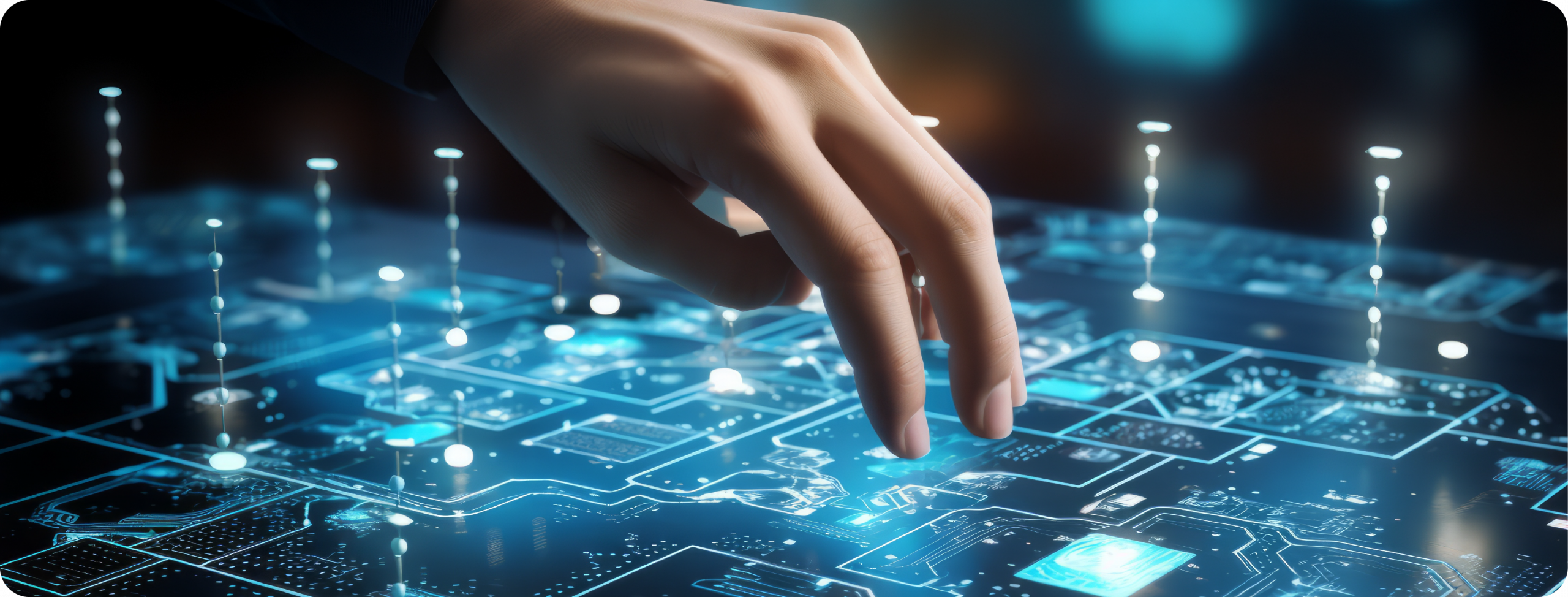
Summary
The future of business is software-centric. Therefore, it only becomes critical for enterprise leaders to prioritize robust Verification and Validation (V&V). The key lies in virtualization – enabling efficient testing and development cycles. Discover how Bosch SDS’ three-step approach is helping various industries bring unparalleled efficiency and speed to the software-defined V&V lifecycle.
Introduction
The demand for software-defined solutions is rising in today’s fast-paced technological landscape. As industries increasingly rely on software-driven systems, the need for efficient Verification and Validation (V&V) processes has become paramount.
Virtualization in V&V: A Game-Changer in the Field
In an era of software-defined engineering and hi-tech products, reduced dependency on physical systems and hardware becomes a prerequisite. Therefore, virtualization in V&V allows products and solutions to be tested, adapted, and improved while they are still being developed – through easier, faster, and more reliable means.
Virtualization in V&V can be achieved in multiple steps and at various scales as required. However, to accrue greater benefits, the right strategic partner is crucial to help map the process steps and achieve this technology-enabled transformation.
Here, Bosch Software and Digital Solutions (SDS) emerges as a leader with an array of cutting-edge solutions for software-defined V&V. Let’s deep dive into our three-step approach:
Figure 01: Steps for Bosch SDS in Transforming to a Software-Defined V&V
Step 01: Virtualize
Virtualization is the process of transforming test systems into a non-hardware-based system where complete testing can be performed in a PC environment. At Bosch SDS, virtualization is achieved in two steps: Virtual ECU (vECU) generation and its integration with other components.
First, take a quick glance at how vECUs are categorized.
Now, take a look at the various characteristics related to these vECUs.
Figure 02: Types of vECU
Post vECU generation, the next step is to integrate it into a Co-Simulation middleware.
To enable this, all the artifacts (i.e., Plant Models, Sensor Models, REST Bus Models, and vECUs) are converted into a standard format called .fmu, which is fmi-compliant. There are multiple tools that can integrate fmi-compliant artifacts and run Co-Simulation. This environment can be used for Test Automation and can also be deployed into the cloud to achieve V&V at scale.
Figure 03: Multi-ECU Co-Simulation Environment
Bosch SDS offers various toolchains and methods for vECU generation, Plant Model adaptations, integration, and Co-Simulation.
Step 02: Automate
Automation in testing is not a new concept. Test Automation has been running in Hardware in Loop (HiL) systems for ages and is extensively used across industries. However, the time has come to automate the whole test lifecycle, starting with Software Build, Integration Testing, and Reporting. Sounds like DevOps?
The traditional IT industry has been automating software development through DevOps for quite some time, and it has become a normal practice. A robust DevOps cycle ensures earlier defect detection, a quick feedback cycle, and more frequent software releases while ensuring quality.
Figure 04: Bosch SDS’ DevOps Automation stages
Bosch SDS offers standalone DevOps solutions in the field of Embedded Engineering where all the software development process steps can be automated.
Step 03: Scale
Even with the high degree of virtualization and automation in the software development lifecycle, the task is far from over. It is imperative to collaborate across organizational boundaries where multiple stakeholders are contributing to one software release. Simply put, systems need to move to the cloud to ensure a high degree of automation, scale, and collaboration.
Cloudification in V&V provides many new possibilities like Remote Testing, Parallel Testing and Test Farm. These eventually help save on cost and time associated with conventional testing.
Benefits of Virtualization
The varied advantages of absolute virtualization can be realized at different levels of system engineering V-model.
Figure 05: Direct and indirect benefits of virtualization in V&V
Bosch SDS has multiple cloud offerings where parallel simulation, execution, and DevOps can be achieved. We can help enable a quick testing cycle and reduce defect leakages.
Way Forward with Bosch SDS
By embracing virtualization technologies and leveraging advanced methodologies, Bosch SDS empowers organizations to accelerate innovation, mitigate risks, and deliver superior products to market.
As industries continue to embrace digital transformation, Bosch SDS stands ready to usher in a new era of software-defined V&V excellence – backed by years of expertise and successful customer stories.
We are uniquely positioned to readily aid enterprises seeking to navigate the complexities of software-defined V&V and remain committed to helping drive innovation, deliver value, and exceed customer expectations.