Defining a Business Case and ROIs for Factories of the Future
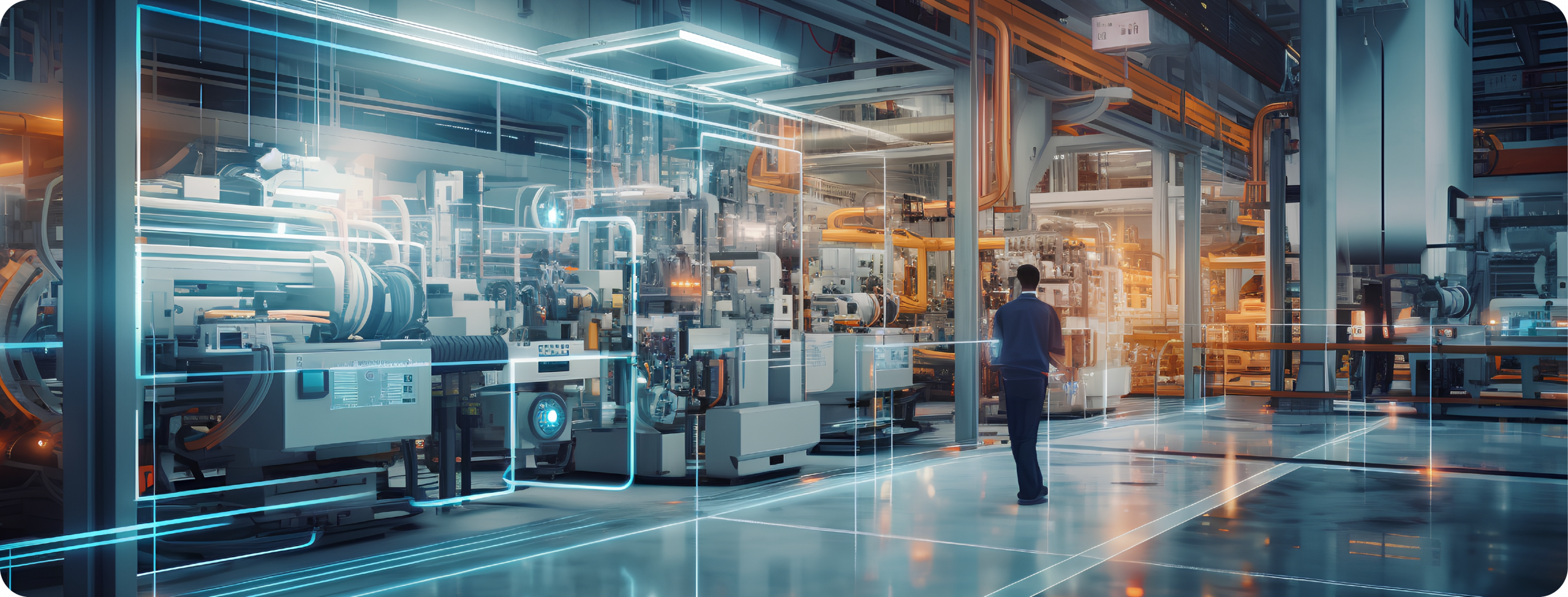
Summary
Manufacturing transformation goes beyond automation, focusing on maximizing throughput, minimizing downtime, and enhancing sustainability. Bosch explores how businesses can define clear ROI for digital investments by considering factors like reduced production cycle times, optimized space utilization, and lower resource consumption. In this blog, discover how IT-OT integration, robotics-as-a-service, and a strong innovation culture help enterprises accelerate their transition to the factories of the future while fostering continuous learning and workforce upskilling.
Introduction
The driving forces shaping the ‘Factories of the Future’ are digital technologies like automation, utility monitoring, shopfloor management systems and “shopfloor to top floor” connectivity. As businesses expand, the inevitability of digitalization for sustainable growth is evident, yet there is a diverse range of opinions regarding its associated benefits. Often companies struggle to define a clear ROI roadmap for their digital investments. In this article, we plan to cover some of the key points to keep in mind while creating the business plan for Manufacturing Transformation.
Redifining ROI for digitalization
Let’s begin by dispelling a myth: “Digitalization programs are not solely focused on reducing the workforce or associated cost.” If this perspective is the sole basis for calculating return on investment (ROI), the results are likely to be unimpressive. When determining the ROI for such investments, it is crucial to factor in both the ‘cost of doing nothing’ and the ‘opportunity cost of transformation’.
To achieve Manufacturing Transformation or establish the ‘Factories of the Future,’ it is essential to focus on enhancing throughput and the benefits derived from it. For instance, this may manifest as decreased production cycle times or improved space utilization through increased automation.
- A reduced production cycle time can decrease the inventory holding cost and free up working capital for organizations.
- Space reduction can help set up smaller factories thus helping save the real-estate cost and increase the throughput/sq ft of an existing plant space.
- Closed loop systems can help reduce resource consumption and thus lead to savings in indirect material cost.
- Minimizing unplanned downtime or implementing scheduled downtime is instrumental in mitigating losses and avoiding production shortfalls. Planned downtimes directly influence Mean Time To Repair (MTTR) and Mean Time Between Failures (MTBF), contributing to an enhanced organizational capability to fulfil delivery commitments to customers.
- Reducing resource consumption for indirect resources used in the manufacturing process like Water, Air, Gas, Energy and Steam lead to not just direct dollar savings but also help organizations move forward in their sustainability and “Net-Zero” journey.
The Intangible Benefits of Manufacturing Transformation
From a statistical standpoint, industrial automation and associated technologies (like computer vision, IIOT, advanced analytics etc.) can contribute to lowering instances of quality failures, consequently reducing quality-related costs for the organization. Simultaneously, they play a role in safeguarding the brand reputation and value of the company.
Prioritizing worker safety is a paramount concern, and rightfully acknowledged as such. Embracing automation can significantly reduce the expenses linked to worker safety, thereby enhancing the overall resilience of the business. This is especially vital in dealing with unforeseen events such as the COVID-19 pandemic or the complexities stemming from the widespread global labor shortages.
It is also important to consider that the business models around manufacturing digitization are continuously changing and evolving thereby supporting easier and quicker deployment without burning a hole in the pockets. As an example, on the automation topic- organizations are already exploring robotics-as-a-service and are considering robots as temporary workers to ramp up production and shipments for a sporadic demand increase. They offer an easy alternative allowing faster ramp-up and ramp-down without making massive capital commitments.
Another key challenge that companies face is around ensuring a perfect IT-OT integration, with the diverse machines and equipment sets on the shopfloor or Level 0 systems, connectivity may become a big challenge. It is therefore necessary to choose systems and solutions that allow easy connectivity despite the equipment diversity on your shopfloor to provide the “Shop Floor to Top Floor” connectivity.
Positioning innovation as the focal point is imperative for manufacturing transformation. Organizations should actively cultivate a culture of innovation within their ranks. Establishing an innovation process is key to nurturing this culture within the organization. As a first step to building an innovation culture, the organizations must create an innovation process.
An innovation process facilitates the objective and transparent assessment of ideas. It should be structured in a manner that distinguishes between a “Dreamer” and an “Innovator.”
Fostering an innovation culture involves encouraging openness or candor and recognizing that valuable ideas can originate from anyone within the organization. Establishing mechanisms for collecting and evaluating ideas properly is crucial.
Conclusion
Finally, it is also important to note that the advent of automation will lead to the creation of new job roles and titles, presenting opportunities for employees to reskill and upskill. Organizations should create a supportive environment for facilitating employee reskilling. Along with their transformation into the “Factories of the Future” – Organizations should consider transforming into a learning-oriented entity that fosters continuous learning, upskilling, and individual employee transformation as well.